- SMC Home
- Products
- Electric Actuators
- Actuators with Battery-less Absolute Encoders
Actuators with Battery-less Absolute Encoders
SMC has introduced a line of actuators driven by 24VDC step motors fitted with battery-less absolute encoders. An absolute encoder offers position data upon power-on, avoiding the homing routine an incremental encoder requires. Our battery-less absolute encoder pairs orientation sensors with differently sized rotating wheels to enable position detection. This electro-mechanical design eliminates the battery and its accompanying import and disposal restrictions common to traditional absolute encoders. A battery-less solution is also free of memory retention limits from extended power-off situations.
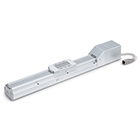
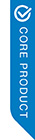
LEFS Slider, Ball Screw Drive, Battery-less Absolute Encoder
The rodless LEFS slider is an electric actuator with a load mounting platform situated above a ball screw drive. A flexible seal band permits platform travel while preventing foreign matter from entering the drive. Slider advantages include a low profile height, shorter length than a rod with equivalent stroke, and better positioning repeatability than a belt driven slider. This version includes a 24VDC motor with a battery-less absolute encoder. This encoder allows the actuator to be powered down without losing its positional awareness. The machine's PLC can access the controller's operational and positional step data through several fieldbus protocols, IO-Link, or parallel I/O.
- Body sizes: 25, 32, 40
- Maximum work load: 65 kg
- Maximum speed: 1200 mm/s
- Stroke range: 50 to 1200mm in 50mm increments
- Positioning repeatability: ±0.02mm, or ±0.015mm (high precision)
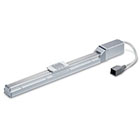
LEFS Ball Screw Slider, High Performance with Battery-less Absolute Encoder
LEFS*G is a high performance version of the standard slider, also equipped with the battery-less encoder onboard the motor. This encoder allows the actuator to be powered down without losing its positional awareness. Further, battery replacement and recycling are eliminated. Load capacities have increased 9-50%. Cycle time is dramatically reduced by a combination of higher maximum speed and acceleration/deceleration. Note that maximum speed gains are primarily in the 50-400mm stroke range, ranging from 5-36% faster depending on motor size and ballscrew pitch. The LEFS*G actuator pairs with a high performance step motor controller, the JXC*H. Actuator dimensions and mounting are identical to the standard LEFS, allowing an updgrade for exisiting equipment
- Body sizes: 16, 25, 32, 40
- Stroke range: 50 to 1200mm in 50mm increments
- Maximum work load: 75 kg (horizontal); 25 kg (vertical)
- Maximum speed: 1500mm's (H lead, size 25)
- Maximum acceleration: 10,000 mm/s² (horizontal); 5,000 mm/s² (vertical)
- Positioning repeatability: ±0.02mm (±0.015mm high precision type)
- Motor type: 24 VDC step motor with battery-less absolute encoder
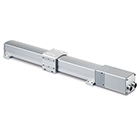
LEFSW Slider, IP65 Dust and Water Resistant, Battery-less Absolute Encoder
LEFSW is a ballscrew slider designed with IP65 equivalent features. The loading table is mounted to the drive underneath the body to limit ingress of liquid and particulate contamination falling from above. Wear resistant seal bands along the stroke path also block dust and water from entering. Supplying air pressure to the purge port creates another barrier to foreign matter and humidity. The motor is enclosed by a dust and splashproof sealed cover. Threaded metal connectors avoid contaminant entry while increasing the strength and rigidity of the electrical connection. The internal ballscrew, rail guide and other metal parts are treated for corrosion resistance, while moving parts are supplied with water-resistant grease. Brackets are available for foot, ceiling or wall mounting.
- IP65 equivalent enclosure
- Sealed motor cover with metal cable connectors
- Battery-less absolute encoder holds position data without power
- Available size: 16, 25, 32, 40
- Max stroke length: 1200mm (size 40)
- Max work load: 65 kg (size 40)
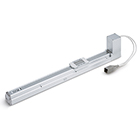
LEFB Belt Drive Slider, Battery-less Absolute Encoder
The rodless LEFB slider is an electric actuator with a load mounting platform situated above a belt drive. A flexible seal band permits platform travel while preventing foreign matter from entering the drive. Slider advantages include a low profile height, shorter length than a rod with equivalent stroke, plus longer strokes and higher speeds than a ball screw driven slider. This version includes a 24VDC motor with a battery-less absolute encoder. This encoder allows the actuator to be powered down without losing its positional awareness. The machine's PLC can access the controller's operational and positional step data through several fieldbus protocols, IO-Link, or parallel I/O.
- Body sizes: 16, 25, 32
- Maximum work load (horizontal only): 19 kg
- Maximum speed: 1500 mm/s
- Stroke range: 300 to 2000mm in 100mm increments
- Positioning repeatability: ±0.08mm
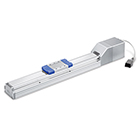
LEKFS*E High Rigidity Slider, Ball Screw Drive, Battery-less Absolute Encoder
The rodless LEKFS*E slider is an electric actuator with a load mounting platform situated above a ball screw drive. A flexible seal band permits platform travel while preventing foreign matter from entering the drive. Slider advantages include a low profile height, shorter length than a rod with equivalent stroke, and better positioning repeatability than a belt driven slider. LEKFS*E includes a redesigned guide with 4 rows of steel balls instead of 2, improving both allowable moment rigidity and positioning repeatability. Additional enhancements vs. the LEFS include auto switch mounting grooves, improved dustproof performance with magnetic seal band adhesion, standard positioning pin holes and drop-in upgrade replacement vs. LEFS. The LEKFS*E also features a 24VDC motor with a battery-less absolute encoder. This encoder allows the actuator to be powered down without losing its positional awareness. The machine's PLC can access the controller's operational and positional step data through several fieldbus protocols, IO-Link or parallel I/O.
- Body sizes: 16, 25, 32, 40
- Maximum work load: 65 kg
- Maximum speed: 1200 mm/s
- Stroke range: 50 to 500mm in 50mm increments, 600-1200mm in 100mm increments
- Positioning repeatability: ±0.01mm, or ±0.02mm (high speed screw lead)
- Dynamic allowable moment: 8-61% improved vs. LEFS (size and axis dependent)
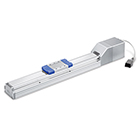
LEKFS*G High Rigidity Slider, Ball Screw Drive, High Performance with Battery-less Absolute Encoder
The LEKFS*G slider is the high performance version of the standard LEKFS*E. This motor upgrade improves the maximum work load, maximum acceleration, and maximum velocity compared to the standard motor. Lower cycle times can be realized with the higher performance. All other features of the LEKFS*E are included.
- Body sizes: 25, 32, 40
- Maximum work load: 75 kg
- Maximum speed: 1300 mm/s
- Stroke range: 50 to 500mm in 50mm increments, 600-1200mm in 100mm increments
- Positioning repeatability: ±0.01mm, or ±0.02mm (high speed screw lead)
- Dynamic allowable moment: 8-61% improved vs. LEFS (size and axis dependent)
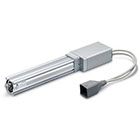
LEY*G, High Performance Rod, Absolute Batteryless Encoder
LEY*G is a high performance version of the standard rod actuator, suitable for push, pull, lift and press applications. Cycle time is dramatically reduced by a combination of higher maximum speed and acceleration/deceleration. Speed gains are 20-60% faster, depending on motor size, ballscrew pitch, and stroke. The 24VDC motor also includes a battery-less absolute encoder, allowing the actuator to be powered down without losing its positional awareness. Replacement battery inventory and end-of-life recyclilng efforts are no longer necessary. Motor operation is provided by the JXC*H High Performance controller line, with PLC, IO-Link or Ethernet fieldbus protocol interfaces. Actuator dimensions and mounting are identical to the standard LEY, alowing an upgrade for existing equipment. I/O and actuator cables are also identical to the standard LEY.
- Body sizes: 16, 25, 40
- Maximum work load: 100 kg (horizontal); 46 kg (vertical)
- Maximum speed: 800 mm/s (16mm lead, size 40)
- Maximum acceleration: 10, 000 mm/s ²
- Stroke range: 30 to 500mm in 50mm increments
- Positioning repeatability: ±0.02mm
- Motor type: 24 VDC step motor with absolute batteryless encoder
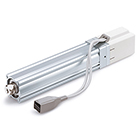
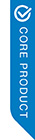
LEY*E Rod, Battery-less Absolute Encoder
The LEY rod electric actuator is suitable for push, pull, lift and press applications. The motor orientation can be reverse mounted on top for compact length, or inline for compact height. Several mounting options are available to accommodate a range of machine requirements. This version includes a 24VDC motor with a battery-less absolute encoder. This encoder allows the actuator to be powered down without losing its positional awareness. The machine's PLC can access the controller's operational and positional step data through several fieldbus protocols, IO-Link, or parallel I/O.
- Body sizes: 16, 25, 32, 40
- Maximum work load: 90 kg (horizontal); 53 kg (vertical)
- Maximum pushing force: 1058 N
- Maximum speed 500 mm/s
- Maximum stroke: 500mm
- Positioning repeatability: ±0.02mm
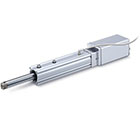
LEY-X8 Rod, IP67 Dust/Waterjet Proof, Battery-less Absolute Encoder
The X8 option is a dust-proof and water-jet-proof specification equivalent to IP67. This spec is achieved with the addition of several unique features above the standard LEY. The motor is sealed within an aluminum cover, fitted with M-type metal cable connectors. The rod passes through a scraper and employs a lubrication retainer to prevent oil film washout. Futher, grease supply holes are also provided. The body extrusion includes a vent hole and fitting to balance internal pressure so that dust and water are not drawn in. The 24VDC motor includes a battery-less absolute encoder. This encoder allows the actuator to be powered down without losing its positional awareness. The controllers's operational and positional step data can be accessed through several fieldbus protocols, IO-Link, or parallel I/O. Available in body sizes 25, 32, and 40.
- Same load and performance as standard LEY
- IP67 environmental protection rating
- Sealed aluminum motor cover with metal cable connectors
- Rod scraper with lube retainer
- Grease supply holes
- Body vent hole
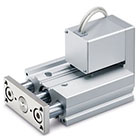
LEG, High Rigidity Guide Rod, High Performance, Battery-less Absolute Encoder
LEG is a rod actuator featuring a guide body with two guide rods and a front tool plate. This is the electric version of our well-known MGP pneumatic guided actuator. Guide rod diameters and bushings are larger than those available in the LEYG, offering improved rigidity. The guide rods stabilize the actuator and support offset loads, making LEG suitable as a conveyor stopper, or for lifting or pushing larger objects. The compact extruded body also has grooves for mounting external position sensors. The 24VDC motor includes a battery-less absolute encoder, allowing the actuator to be powered down without losing its positional awareness. Replacement battery inventory and end-of-life recycling efforts are no longer necessary. Motor operation is provided by the JXC*H High Performance controller line, with either PLC or Ethernet fieldbus protocol interfaces.
- Body sizes: 25, 32, 40
- Maximum work load: 60 kg (horizontal); 27 kg (vertical) (size 40)
- Maximum pushing force: 553 N (size 40)
- Maximum speed: 250 mm/s (size 25)
- Maximum stroke: 100mm
- Positioning repeatability: ±0.02mm
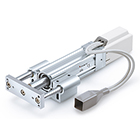
LEYG Guided Rod, Battery-less Absolute Encoder
The LEYG guided rod electric actuator pairs a LEY actuator with a bolt-on bearing block with double guide rods. The guide rods counter rotational forces instead of the drive and motor, and also resist shock and sustained lateral loads. Guide selection offers either slide or ball bushing bearings. The motor orientation can be reverse mounted on top for compact length, or inline for compact height. This version includes a 24VDC motor with a battery-less absolute encoder. This encoder allows the actuator to be powered down without losing its positional awareness. The machine's PLC can access the controller's operational and positional step data through several fieldbus protocols, IO-Link, or parallel I/O.
- Body sizes: 16, 25, 32, 40
- Maximum work load: 90 kg (horizontal; 51 kg (vertical)
- Maximum pushing force: 1058 N
- Maximum speed: 500 mm/s
- Maximum stroke: 300mm
- Positioning repeatability: ±0.02mm
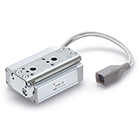
LES Slide Table, Compact, Battery-less Absolute Encoder
The LES electric actuator combines a motor and ball screw drive, worktable, and linear guide in compact body. The formed sheet metal table allows a lower mounting surface height, lighter weight, and greater vertical work load than the LESH slide table. Body orientations include basic, symmetrical, and inline mounted motor. This version includes a 24VDC motor with a battery-less absolute encoder. This encoder allows the actuator to be powered down without losing its positional awareness. The machine's PLC can access the controller's operational and positional step data through several fieldbus protocols, IO-Link, or parallel I/O.
- Body size: 25
- Maximum work load: 5 kg (horizontal or vertical)
- Maximum pushing force: 180 N
- Maximum speed: 400 mm/s
- Strokes: 30, 50, 75, 100, 125, 150mm
- Positioning repeatability: ±0.05mm
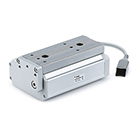
LESH Slide Table, High Rigidity, Battery-less Absolute Encoder
The LESH electric actuator combines a motor and ball screw drive, worktable, and linear guide in compact body. The machined table is more rigid than the LES formed table, enabling higher horizontal loads and improved deflection from offset loading. Body orientations include basic, symmetrical, and inline mounted motor. This version includes a 24VDC motor with a battery-less absolute encoder. This encoder allows the actuator to be powered down without losing its positional awareness. The machine's PLC can access the controller's operational and positional step data through several fieldbus protocols, IO-Link, or parallel I/O.
- Body size: 25
- Maximum work load: 9 kg (horizontal), 4 kg (vertical)
- Maximum pushing force: 180 N
- Maximum speed: 400 mm/s
- Strokes: 50, 100, 150
- Positioning repeatability: ±0.05mm
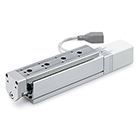
LESYH, Electric Slide Table, High Precision Type, Battery-less
The LESYH is a high precision variation of the LESH high rigidity slide table. This actuator improves positioning repeatability to ± 0.01 and increases vertical work load dramatically compard to the LESH. The external motor can be mounted inline with the table, or in parallel to the left or right. This version includes a 24VDC step motor with a battery-less absolute encoder. This encoder allows the actuator to be powered down without losing its positional awareness. The machine's PLC can access the controller's operational and positional step data through several fieldbus protocols, IO-Link, or parallel I/O.
- Body size: 8, 16, 25
- Strokes: 50, 75, 100 or 150mm
- Maximum work load: 12 kg (horizontal, 20 kg (vertical))
- Maximum pushing force: 420 N
- Maximum speed: 400 mm/s
- Positioning repeatability: ±0.01mm
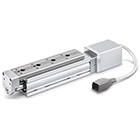
LESYH*G, High Precision Slide Table, High Performance with Battery-less Absolute Encoder
The LESYH*G improves on the high precision LESYH slide table by adding a higher performance 24VDC step motor. This motor also includes a battery-less absolute encoder, which allows the actuator to be powered down without losing its positional awareness. The LESYH*G offers the most superlative features in the LES line including the highest acceleration / deceleration, highest speed, highest load capacities, and highest pushing force. The external motor can be mounted inline with the table, or in parallel to the left or right. The JXC*H motor controller options include Ethernet fieldbus protocol compatibility or parallel input from the machine's PLC.
- Body size: 8, 16, 25
- Strokes: 50, 75, 100, or 150mm
- Maximum work load: 12 kg (horizontal), 20 kg (vertical)
- Maximum pushing force: 765 N
- Maximum speed: 800 mm/s
- Maximum accel / decel: 10,000 (horizontal), 5,000 (vertical) mm/s²
- Positioning repeatability: ±0.01mm
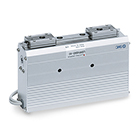
LEHF Gripper, Battery-less Absolute Encoder
The LEHF gripper uses a belt driven slide shaft to open and close the fingers. The low profile, flat fingers follow a linear guide for alignment and stability. The body and drive construction permit long strokes, suitable for gripping larger items without excessive moment loading. This version includes a 24VDC motor with a battery-less absolute encoder. This encoder allows the actuator to be powered down without losing its positional awareness. The machine's PLC can access the controller's operational and positional step data through several fieldbus protocols, IO-Link, or parallel I/O.
- Body sizes: 32, 40
- Stroke range: 32 or 40mm (basic); 64 or 80mm (long)
- Gripping force range: 48 to 180 N
- Repeatability: ±0.05
- Low profile fingers
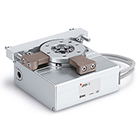
LER Rotary Table, Battery-less Absolute Encoder
The LER features a rotating worktable positioned above an enclosure for the motor and drive train. Both a basic and high torque variation are offered. Three rotation angles are also available, including 90°, 180°, or 320°. This version includes a 24VDC motor with a battery-less absolute encoder. This encoder allows the actuator to be powered down without losing its positional awareness. The machine's PLC can access the controller's operational and positional step data through several fieldbus protocols, IO-Link, or parallel I/O.
- Body size: 50
- Rotation angles: 320°, 90° or 180° (external stopper)
- Maximum torque: 6.6 N?m (basic), 10 N?m (high)
- Positioning repeatability: ±0.05° (±0.01° at end with external stopper)
- Backlash: ±0.5°
Product & CAD Models
- Actuators
- Directional Control Valves
- Airline Equipment
- Air Dryers Main Line Filters
- Connectors
- Vacuum Products
- Industrial Communication
- Sensors Switches Controllers
- Fluid Process
- Static Control
-
Electric Actuators
- Electric Actuators
- Actuators with Integrated Controllers
- Actuators with Battery-less Absolute Encoders
- Actuators for Manifold Controller
- Sliders
- AC Servo Sliders
- Rod Guided Rod
- AC Servo Rod
- Slide Tables
- AC Servo Slide Table
- Rotary Table
- Electric Grippers
- Miniature
- Controllers Drivers
- Clean Room Products
- Chillers
- Process Gas Equipment
- High Vacuum
- Chemical Handling Equipment
- Cobot Gripping Solutions
- Secondary Battery